What are the advantages and disadvantages of carbonization furnaces
As a device for converting biomass raw materials into charcoal, carbonization furnace has its unique advantages and disadvantages. The following is a detailed analysis of the advantages and disadvantages of carbonization furnaces:
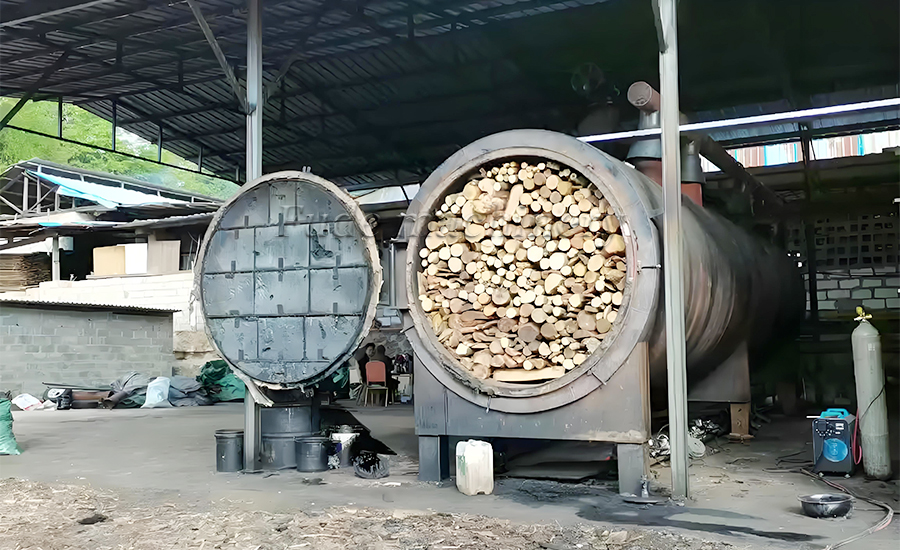
advantage
- Efficient and energy-saving:
- The carbonization furnace can achieve high-temperature, continuous, and multi-layer carbonization technology, thereby improving production efficiency.
- During the carbonization process, the combustible gases generated can be recovered and re burned, providing heat energy for the carbonization furnace and reducing energy consumption.
- Environmentally friendly and smoke-free:
- The new environmentally friendly carbonization furnace is equipped with a flue gas recovery device, which can purify the flue gas generated during the carbonization process to achieve dust-free and smoke-free standards.
- The recycled flue gas can also be converted into combustible gas for heating, cooking, or drying, achieving the reuse of resources.
- One machine dual-use:
- The carbonization furnace has two functions: direct carbonization of materials and pre carbonization of rods, which meet different material and production needs.
- Automated control:
- Carbonization furnaces are usually equipped with electric control cabinets and intelligent control systems, which can achieve automated production and reduce labor intensity.
- High carbonization rate and high yield:
- The carbonization rate of the carbonization furnace is high, and it can convert most materials into charcoal.
- At the same time, the yield of carbonization furnaces is also high, and the quality of the produced charcoal is stable and reliable.
disadvantage
- High initial investment:
- The manufacturing cost of carbonization furnace is relatively high, so its market price is also relatively high. For small businesses or individuals, the initial investment may be significant.
- Maintenance cost:
- During long-term use, carbonization furnaces require regular maintenance and upkeep. This includes checking the operating status of the equipment, replacing worn parts, etc., all of which will increase maintenance costs.
- High operational technical requirements:
- Although the carbonization furnace is equipped with an automated control system, operators still need to have certain professional knowledge and technical experience. If operated improperly, it may affect the normal operation of the carbonization furnace and the quality of charcoal.
- Limited adaptability to raw materials:
- Carbonization furnaces are mainly suitable for materials containing lignin, such as sawdust, wheat straw, etc. For other types of raw materials, such as plastics, rubber, etc., carbonization furnaces may not be able to process them or the processing effect may be poor.
- Limitations of intermittent carbonization furnace:
- Intermittent carbonization furnaces require manual loading and unloading of materials during the carbonization process, which may result in lower production efficiency. Meanwhile, due to the material being fixed in the furnace, uneven carbonization may occur.
In summary, the carbonization furnace has the advantages of high efficiency, energy saving, environmental protection, smoke-free, dual-use, automatic control, and high carbonization rate. However, it also has disadvantages such as high initial investment, maintenance costs, high operational technical requirements, limited adaptability to raw materials, and limitations of intermittent carbonization furnaces. When choosing a carbonization furnace, it is necessary to comprehensively consider one’s own production needs, economic conditions, and technological level.
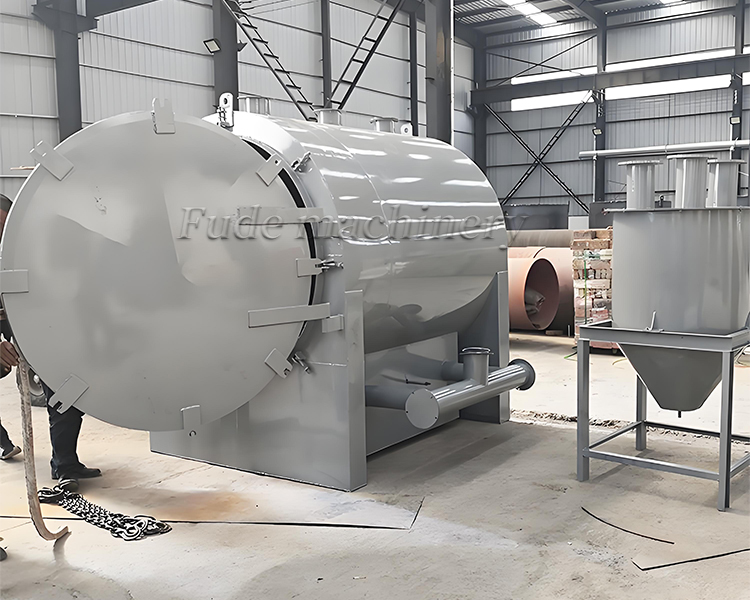
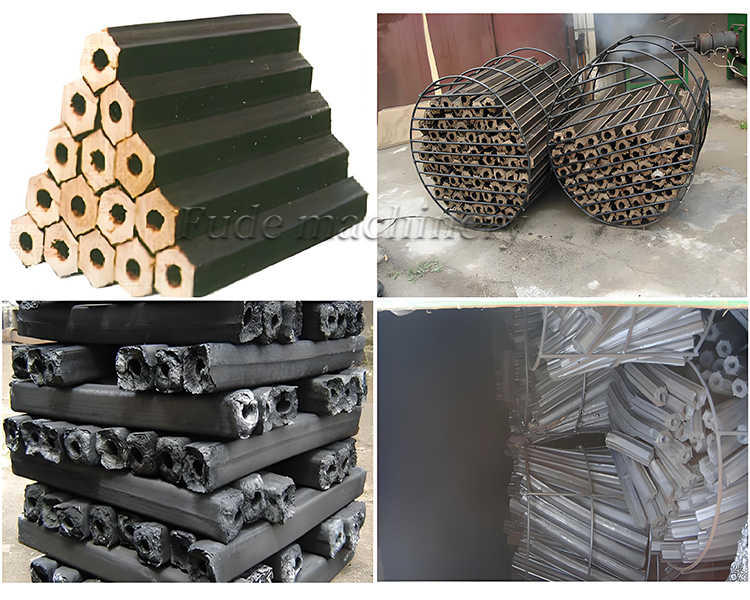